Giriiş :
Die döküm takımları, metal döküm endüstrisinde, yüksek hassasiyet ve tekrarlanabilirliğe sahip karmaşık geometriler ürettiği bilinen önemli bir bileşendir. Bu verimli ve çok yönlü yöntem, minimum işleme gereksinimlerine sahip parçalar üretmek için yeniden kullanılabilir kalıplardan yararlanır.
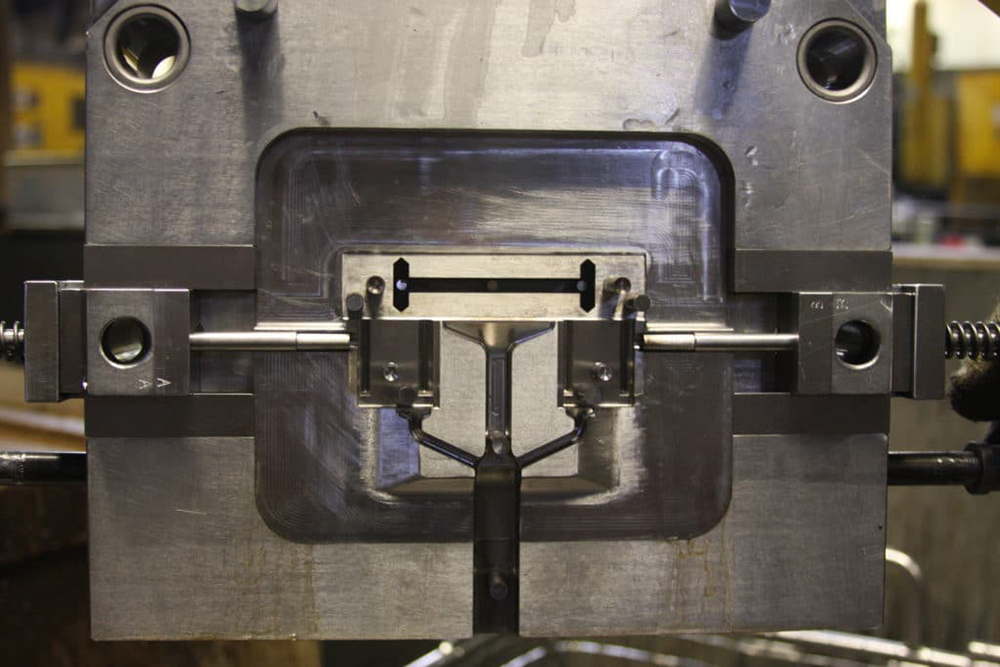
Die döküm takımı nedir?
Die Döküm Takımlarıkalıp döküm işleminde kullanılan kalıpları veya araçları ifade eder. Bu kalıplar, yüksek basınçlı erimiş metal enjeksiyonu yoluyla metal bileşenler oluşturmak için tasarlanmıştır. Die döküm takımlarında kullanılan anahtar malzemeler şunları içerir:
Ayrıntılı parçaları verimli bir şekilde üretme yeteneği nedeniyle otomotiv, havacılık ve elektronik gibi endüstrilerde kalıp döküm takımları gereklidir.
Die döküm takımlarının adım adım işlemi
1. Kalıp Hazırlığı
Kalıp hazırlama aşaması, yüksek kaliteli döküm parçaları elde etmek için çok önemlidir. Uygun kalıp tipini seçmek üretim ihtiyaçlarınıza bağlıdır. Örneğin, tek boşluklu kalıplar, döngü başına bir parça üretmek için idealdir ve daha küçük üretim çalışmaları için ayrıntılı hassasiyet sağlar. Bu arada, çoklu boşluklu kalıplar aynı anda birden fazla özdeş parça oluşturarak üretkenliği artırır. Çok yönlülük gerekiyorsa, kombinasyon kalıpları tek bir kalıpta birden fazla parça tasarımına izin verir. Ekler veya ince duvarlar gerektiren karmaşık parçalar için birim kalıplar özel çözümler sunar.
Kalıp tipi seçildikten sonra, kalıbın temizlenmesi ve önceden ısıtılması önemli adımlardır. Temizlik, metalin akışını tehlikeye atabilecek veya kusurlarla sonuçlanabilecek kirleticileri giderir. Kalıbın önceden ısıtılması sıcaklığını stabilize eder, termal şok riskini en aza indirir, bu da çatlaklara veya yüzey kusurlarına neden olabilir. Bu hazırlık optimal metal akışını sağlar ve kalıbın dayanıklılığını arttırır.
2. Enjeksiyon işlemi
Enjeksiyon işlemi, kullanılan metal tipine göre değişir. Sıcak oda kalıp dökümü için, yaygın olarak çinko ve magnezyum gibi düşük eritilen metallerle uygulanan erimiş metal, doğrudan makinenin fırından kalıp boşluğuna çekilir. Bu yöntem, hızlı üretim döngüleri sunar ve manuel kullanımı en aza indirir, bu da küçük ve orta boy bileşenler verimli bir şekilde üretmek için idealdir.
Buna karşılık, soğuk oda kalıp dökümü, alüminyum ve bakır gibi daha yüksek erime noktalarına sahip metaller için tasarlanmıştır. Bu metaller aşırı ısı gerektirdiğinden, erimiş metal, kalıp yüksek basınç altında enjekte edilmeden önce soğuk odaya manuel olarak atılmalıdır. Bu işlem sıcak oda yönteminden biraz daha uzun sürse de, otomotiv ve havacılık gibi zorlu endüstrilerde kullanılan büyük, sağlam parçalar için gereken dayanıklılığı ve gücü sağlar.
3. Soğutma aşaması
Soğutma fazı, yeni enjekte edilen erimiş metalin kalıp boşluğu içinde doğru bir şekilde katılaşmasını sağlamak için hayati önem taşır. Bu aşamada, metal soğudukça ve istenen şekle sertleştikçe kalıp kapalı kalır. Büzülmeyi en aza indirmek için, soğutma işlemi boyunca kontrollü basınç uygulanabilir, bu da tek tip boyutlar sağlar ve son kısımda iç stres azaltır. Uygun soğutma zamanlaması gereklidir - çok hızlı soğutulursa, parça çatlaklar veya bozulmalar geliştirebilirken, aşırı soğutma süresi üretim verimliliğini azaltabilir. Soğutma aşamasını dikkatlice yönetmek, tutarlı, yüksek kaliteli sonuçlar elde etmenin anahtarıdır.
4. Çıkarma
Metal tamamen katılaştıktan sonra, parça kalıptan çıkarılmalıdır. Bu, sertleştirilmiş metal bileşenini kalıp boşluğundan çıkaran ejektör pimleri kullanılarak elde edilir. Pürüzsüz bir ejeksiyonu kolaylaştırmak için, kalıp tasarımcıları genellikle taslak açılar içerir - parçanın direnç olmadan serbest bırakılmasına yardımcı olan hafif konikler. Ek olarak, uygun küf yağlaması sürtünmeyi en aza indirir, kalıp üzerindeki aşınmayı azaltır ve ömrünü uzatır. Ejeksiyon sürecinin sorunsuz olmasını sağlamak, özellikle yüksek hacimli üretim ortamlarında, parçaya veya kalıpta hasarı önlemek için çok önemlidir.
5. Kesme ve bitirme
Çıkarıldıktan sonra, metal kısım tipik olarak kalıp yarının buluştuğu yerde meydana gelen flaş olarak bilinen fazla malzeme içerir. Bu fazla malzeme, parçanın hassas boyutsal toleransları karşılamasını sağlayarak kırpma yoluyla çıkarılmalıdır. Bileşenin karmaşıklığına bağlı olarak, düzeltme manuel olarak, özel kesme araçları kullanılarak veya daha iyi verimlilik için otomatik işlemler yoluyla gerçekleştirilebilir. Bazı durumlarda, yüzey kalitesini artırmak, dayanıklılığı artırmak veya parçayı montaj için hazırlamak için taşlama, parlatma veya kaplama gibi ek sonlandırma adımları gerekebilir. Profesyonel, kusursuz bir nihai ürün elde etmek için uygun kırpma ve sonlandırma gereklidir.
Die Döküm Türleri Türleri
Sıcak oda ölümü döküm
- Çinko, magnezyum ve düşük eritilen metaller için uygundur.
- Hızlı döngü süreleri ve gelişmiş parça bütünlüğü sunar.
- Elektronik kılıflarda ve küçük hassas parçalarda yaygın olarak kullanılır.
Soğuk oda kalıp döküm
- Alüminyum, bakır ve diğer yüksek eritme noktalı metaller için tasarlanmıştır.
- Otomotiv ve havacılık bileşenleri üretmek için tercih edilir.
- Daha yüksek termal dirençli daha güçlü parçalar sağlar.
Özellik | Sıcak oda ölümü döküm | Soğuk oda kalıp döküm |
Eritme işlemi | Makinenin içinde | Harici fırın gerekli |
Basınç aralığı | 1.000 psi ila 5.000 psi | 1.500 psi ila 25.000 psi |
Yeterlik | Daha hızlı döngü süresi | Daha uzun döngü süresi |
En iyisi | Küçük, ayrıntılı parçalar | Büyük, dayanıklı bileşenler |
Kalıp döküm araçlarını kullanmanın avantajları
- Yüksek hassasiyet: Minimal işleme ile karmaşık geometriler üretir.
- Maliyet verimliliği: Malzeme atıklarını azaltır ve üretimi düzene aktarır.
- Dayanıklılık: Dökme döküm takım malzemeleri yoğun ısı ve basınca dayanır.
- Yüzey kaplaması: Die döküm takımları kullanılarak üretilen parçalar minimum sonlandırma gerektirir.
Die Cast Takımının Gerçek Dünya Uygulaması
Vaka çalışması: otomotiv endüstrisi
Bir otomotiv üreticisi, hafif ve dayanıklı şanzıman kılıfları üretmek için kalıp döküm araçlarını kullandı. Hassas kalıplarla soğuk oda kalıp dökümü kullanarak:
- Malzeme atıklarında% 20 azalma.
- Motor parçalarında gelişmiş termal performans.
- İzci süresi%30 oranında azaltılmıştır.
Bu başarılı uygulama, verimliliği ve ürün kalitesini artırmada kalıp döküm araçlarının rolünün altını çizmektedir.
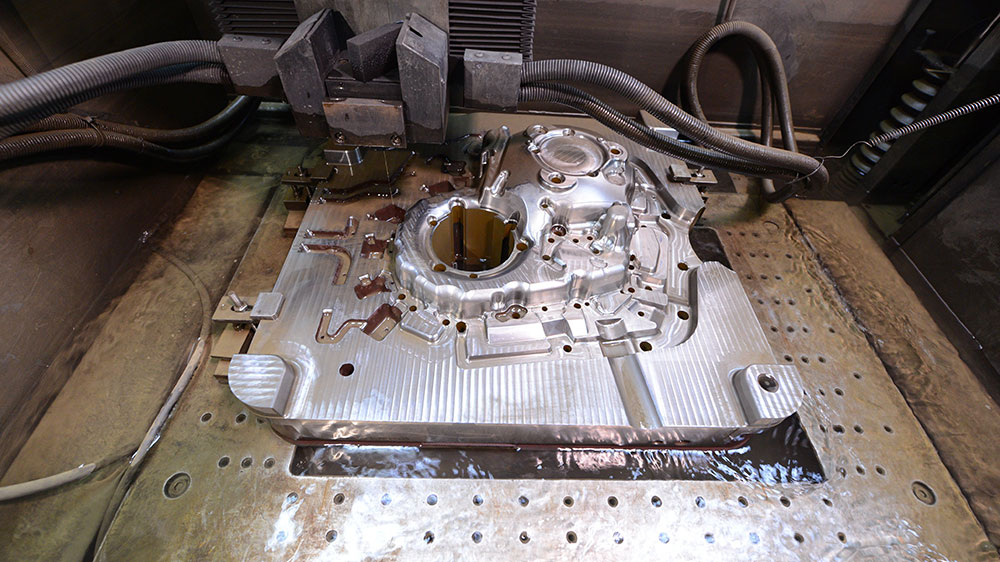
Die döküm takımlarında yaygın zorluklar
Termal yorgunluk
- Çözüm: Geliştirilmiş ısı direncine sahip yüksek kaliteli çelik alaşımlar kullanın.
Metal flaş
- Çözüm: Kelepleme basıncını ve kalıp hizalamasını optimize edin.
Gözeneklilik sorunları
- Çözüm: Enjeksiyon basıncını ve soğutma süresini iyileştirilmiş yoğunluk için ayarlayın.
Çözüm
Die döküm aletleri, hassas ve dayanıklı metal parçaların verimli bir şekilde üretilmesinde hayati bir rol oynar. İster otomotiv, havacılık veya elektronikte olsun, yüksek kaliteli kalıp döküm takımlarına yatırım yapmak, üstün performans ve üretim maliyetlerinin azalmasını sağlar.
Die Cast Takım Hakkında SSS
🛠️ Die döküm takımları için en uygun malzemeler?
Die döküm takımları, yüksek sıcaklıklar, basınç ve mekanik stres gibi aşırı koşullara dayanabilen malzemeler gerektirir. Ortak malzemeler içerirH13 Alet Çeliği, bakır alaşımları, Vemavalanma çeliği.
- H13 Alet Çeliği: Olağanüstü ısı direnci ve dayanıklılığı ile tanınan H13 Tool Steel, yüksek sıcaklıklarda bile sertliğini korur, bu da uzun süreli üretim döngüleri için idealdir.
- Bakır alaşımları: Bu malzemeler, döküm işlemi sırasında soğutma verimliliğini artırmaya yardımcı olan üstün termal iletkenlikleri için tercih edilir. Daha hızlı soğutma, döngü sürelerini azaltır ve parça kalitesini artırır.
- Mavalanma çeliği: Mükemmel tokluk ve stres altında minimum bozulma ile, mıknatıslama çeliği, hassasiyet gerektiren karmaşık kalıplar oluşturmak için uygundur.
Doğru malzemeyi seçmek, takım uzun ömürlülüğünü artırabilir, bakım gereksinimlerini azaltabilir ve ürün tutarlılığını artırabilir.
Die Die döküm takımlarındaki kusurları nasıl azaltabilirim?
Die döküm takımlarındaki kusurları en aza indirmek,Uygun Kalıp Tasarımı, sıcaklık kontrolü, Vebasınç ayarı.
- Kalıp tasarımı: Pürüzsüz malzeme akış yolları, uygun havalandırma ve düzgün duvar kalınlığı sağlamak, gözeneklilik, büzülme ve bükülme gibi sorunları önler.
- Sıcaklık kontrolü: Optimal kalıp ve malzeme sıcaklıklarının korunması, çatlaklara veya eksik dolgulara neden olabilecek termal stresi azaltır. Ön ısıtma kalıpları da kaliteyi tehlikeye atan ani sıcaklık değişimlerini önler.
- Basınç ayarı: Doğru enjeksiyon basıncının uygulanması, erimiş metalin boşlukları veya hava ceplerini bırakmadan her boşluğu doldurmasını sağlar. Enjeksiyon hızının ve basıncının dengelenmesi parça bütünlüğünü optimize eder.
Bu stratejileri birleştirmek, daha iyi ürün tutarlılığı sağlar, yeniden çalışma maliyetlerini ve malzeme israfını azaltır.
Die Die döküm takımı yüksek hacimli üretim için uygun mu?
Kesinlikle! Die Cast Araçları, destekleme yeteneği ile ünlüdüryüksek hacimli üretimtutarlı kaliteyi korurken.
- Dayanıklı takım malzemeleri: H13 Tool Steel ve Maving Çeliği gibi malzemeler, bozulmadan binlerce üretim döngüsüne dayanır.
- Verimli döngü süreleri: Hassas sıcaklık kontrolü ve otomatik işlemlerle, kalıp dökümü hızlı döngü süreleri elde edebilir ve üretim verimliliğini artırabilir.
- Karmaşık parça oluşumu: Die dökme kalıplar, minimum işlem sonrası karmaşık parçalar üretmek için tasarlanmıştır, bu da onları toplu üretim çalışmaları için ideal hale getirir.
Die döküm takımları, sıkı toleranslara ve ayrıntılı özelliklere bağlı kalırken yüksek çıkış üretimi talep eden endüstrilerde mükemmeldir.
🚗 Hangi endüstriler en çok kalıp döküm araçlarından yararlanır?
Die döküm takımı, hassasiyet, dayanıklılık ve ölçeklenebilirliğin anahtar olduğu çeşitli endüstrilerde hayati bir rol oynar:
- Otomotiv endüstrisi: Motor bileşenleri, şanzıman durumları ve mukavemet ve boyutsal stabilite gerektiren yapısal parçalar üretmek için kullanılır.
- Havacılık sektörü: Die Döküm, parantez, muhafazalar ve kontrol sistemi bileşenleri gibi hafif ama sağlam parçalar yaratır.
- Tüketici Elektroniği: Isı lavaboları, konektör muhafazaları ve cihaz çerçeveleri, hassasiyeti ve malzeme çok yönlülüğü nedeniyle kalıp döküm takımlarından yararlanır.
Bu endüstriler, uygun maliyetli, yüksek kaliteli bileşenleri toplu olarak sunma yeteneği için kalıp döküm takımlarından yararlanmaktadır.
Bugün Bize UlaşınUzman Die Cast Araç Çözümlerimizin üretim sürecinizi nasıl geliştirebileceğini ve ürün kalitesini nasıl artırabileceğini öğrenmek için.