Wstęp :
Oprzyrządowanie odlewów Die jest kluczowym elementem w branży odlewów metali, znanych z wytwarzania złożonych geometrii o wysokiej precyzji i powtarzalności. Ta wydajna i wszechstronna metoda wykorzystuje formy wielokrotnego użytku do produkcji części o minimalnych wymaganiach dotyczących obróbki.
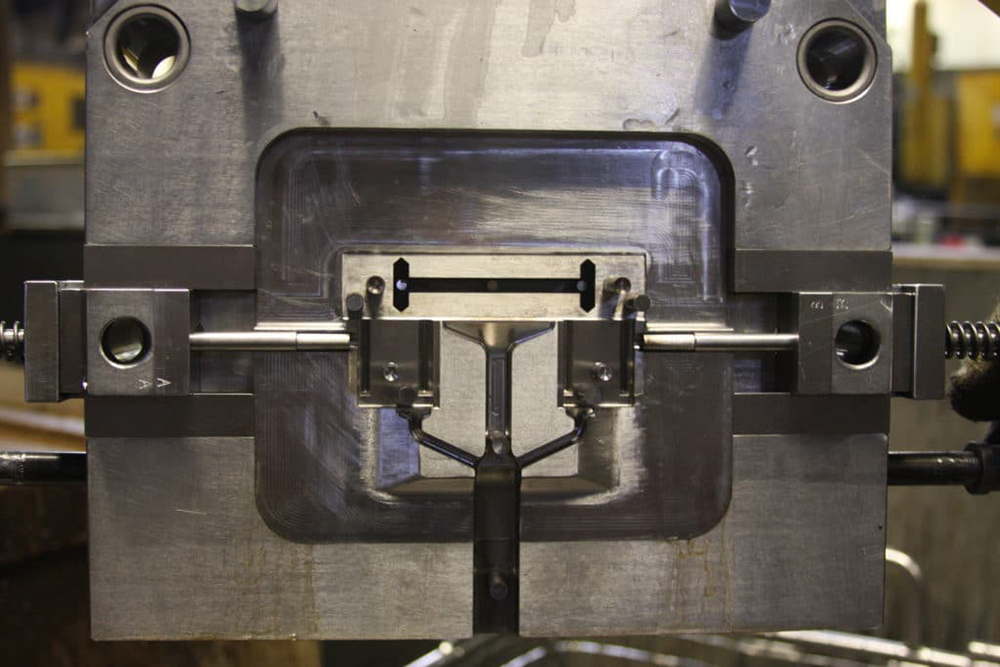
Co to jest narzędzia Die Cast?
Die obsada narzędziodnosi się do form lub narzędzi używanych w procesie odlewania matrycy. Formy te zostały zaprojektowane do tworzenia komponentów metali poprzez pod wysokim ciśnieniem wtrysku stopionego metalu. Kluczowe materiały używane w oprzyrządowaniu odlewu obejmują:
Oprzyrządowanie odlewające die jest niezbędne w branżach, takich jak motoryzacyjna, lotnicza i elektroniczna, ze względu na jego zdolność do wydajnego produkcji szczegółowych części.
Krok po kroku proces narzędzi odlewu
1. Przygotowanie pleśni
Etap przygotowania formy ma kluczowe znaczenie dla osiągnięcia wysokiej jakości części odlewanych. Wybór odpowiedniego typu formy zależy od twoich potrzeb produkcyjnych. Na przykład formy jednorodzinne są idealne do wytwarzania jednej części na cykl, zapewniając szczegółową precyzję dla mniejszych przebiegów produkcyjnych. Tymczasem formy wielokrotności zwiększają wydajność poprzez tworzenie wielu identycznych części jednocześnie. Jeśli wymagana jest wszechstronność, formy kombinowane umożliwiają wiele projektów w jednej formie. W przypadku skomplikowanych części wymagających wkładek lub cienkich ścian formy jednostkowe zapewniają wyspecjalizowane roztwory.
Po wybraniu typu formy czyszczenie i podgrzewanie formy są niezbędnymi krokami. Czyszczenie usuwa zanieczyszczenia, które mogą zagrozić przepływowi metalu lub spowodować wady. Podgrzewanie formy stabilizuje jej temperaturę, minimalizując ryzyko wstrząsu cieplnego, co może powodować pęknięcia lub niedoskonałości powierzchni. To przygotowanie zapewnia optymalny przepływ metalu i zwiększa trwałość pleśni.
2. Proces wstrzyknięcia
Proces iniekcji różni się w zależności od rodzaju stosowanego metalu. W przypadku odlewania matrycy gorącej komory, powszechnie stosowanej z metali o niskiej zawartości topin, takich jak cynk i magnez, stopiony metal jest rysowany bezpośrednio z pieca maszyny do wnęki formy. Ta metoda oferuje szybkie cykle produkcyjne i minimalizuje ręczne obsługi, dzięki czemu jest idealna do wydajnego wytwarzania małych i średnich komponentów.
W przeciwieństwie do tego, odlewanie matrycy zimnej jest przeznaczone do metali o wyższych temperaturach topnienia, takich jak aluminium i miedź. Ponieważ metale te wymagają ekstremalnego ciepła, stopiony metal musi być ręcznie objęty zimną komorą, zanim zostaną wstrzyknięte do formy pod wysokim ciśnieniem. Chociaż proces ten trwa nieco dłużej niż metoda komory gorącej, zapewnia trwałość i siłę wymaganą dla dużych, solidnych części stosowanych w wymagających branż, takich jak motoryzacyjny i lotniczy.
3. Faza chłodzenia
Faza chłodzenia jest niezbędna do zapewnienia nowo wstrzykniętego stopionego metalu poprawnie zestalającą w jamie formy. Na tym etapie pleśń pozostaje zamknięta, gdy metal chłodzi i stwardnieje w pożądanym kształcie. Aby zminimalizować skurcz, kontrolowane ciśnienie można zastosować w całym procesie chłodzenia, zapewniając jednolite wymiary i zmniejszając naprężenie wewnętrzne w końcowej części. Właściwe czas chłodzenia jest niezbędne - jeśli zbyt szybko chłodzone, część może rozwinąć pęknięcia lub zniekształcenia, podczas gdy nadmierny czas chłodzenia może skrócić wydajność produkcji. Staranne zarządzanie fazą chłodzenia jest kluczem do osiągnięcia spójnych, wysokiej jakości wyników.
4. Wyrzucenie
Po całkowitym zestaleniu metalu część należy usunąć z formy. Osiąga się to za pomocą pinów wyrzucających, które wypychają stwardniały element metalowy z wnęki formy. Aby ułatwić płynne wyrzucenie, projektanci pleśni często zawierają kąty szkicu - lekkie zwężenia, które pomagają uwalnianie części bez oporu. Dodatkowo właściwe smarowanie formy minimalizuje tarcie, zmniejszając zużycie formy i przedłużenie jej życia. Zapewnienie bezproblemowego procesu wyrzucania jest kluczowe dla zapobiegania uszkodzeniu części lub formy, szczególnie w środowiskach produkcyjnych o dużej objętości.
5. Przycinanie i wykończenie
Po wyrzuceniu część metalowa zwykle zawiera nadmiar materiału znanego jako Flash, który występuje tam, gdzie spotykają się połówki pleśni. Ten nadmiar materiału należy usunąć przez przycinanie, zapewniając, że część spełnia precyzyjne tolerancje wymiarowe. W zależności od złożoności komponentu przycinanie może być wykonywane ręcznie, przy użyciu wyspecjalizowanych narzędzi tnących lub za pomocą zautomatyzowanych procesów w celu poprawy wydajności. W niektórych przypadkach mogą być wymagane dodatkowe etapy wykończenia, takie jak szlifowanie, polerowanie lub powłoka w celu zwiększenia jakości powierzchni, poprawy trwałości lub przygotowania części do montażu. Właściwe przycinanie i wykończenie są niezbędne do osiągnięcia profesjonalnego produktu końcowego wolnego od wad.
Rodzaje narzędzi odlewu
Gorąca komnata casting
- Nadaje się do metali cynku, magnezu i niskopasmowych.
- Oferuje szybkie czasy cyklu i lepszą integralność części.
- Powszechnie stosowane w obudowach elektronicznych i małych częściach precyzyjnych.
Casting z zimną komnatą
- Zaprojektowany do aluminium, miedzi i innych metali o wysokim punkcie do pomieszczenia.
- Preferowane do produkcji komponentów motoryzacyjnych i lotniczych.
- Zapewnia mocniejsze części o wyższym oporze cieplnym.
Funkcja | Gorąca komnata casting | Casting z zimną komnatą |
Proces topnienia | Wewnątrz maszyny | Wymagany piec zewnętrzny |
Zakres ciśnienia | 1000 psi do 5000 psi | 1500 psi do 25 000 psi |
Efektywność | Szybszy czas cyklu | Dłuższy czas cyklu |
Najlepsze dla | Małe, szczegółowe części | Duże, trwałe komponenty |
Korzyści z korzystania z oprzyrządowania odlewu
- Wysoka precyzja: Wytwarza złożone geometrie przy minimalnej obróbce.
- Wydajność kosztów: Zmniejsza marnotrawstwo materiałowe i usprawnia produkcję.
- Trwałość: Materiały narzędzi odlewu odlewu wytrzymają intensywne ciepło i ciśnienie.
- Wykończenie powierzchni: Części wytwarzane przy użyciu oprzyrządowania odlewu wymagają minimalnego wykończenia.
Realne zastosowanie narzędzi od obsady matrycy
Studium przypadku: przemysł motoryzacyjny
Producent motoryzacyjny wykorzystał oprzyrządowanie odlewów Die do wytwarzania lekkich, ale trwałych obudów skrzyni biegów. Zastosowując odlewanie kości zimnej z precyzyjnymi formami, osiągnęli:
- 20% zmniejszenie odpadów materiałowych.
- Ulepszona wydajność termiczna w częściach silnika.
- Zmniejszony czas realizacji o 30%.
Ta udana aplikacja podkreśla rolę oprzyrządowania odlewania w celu poprawy wydajności i jakości produktu.
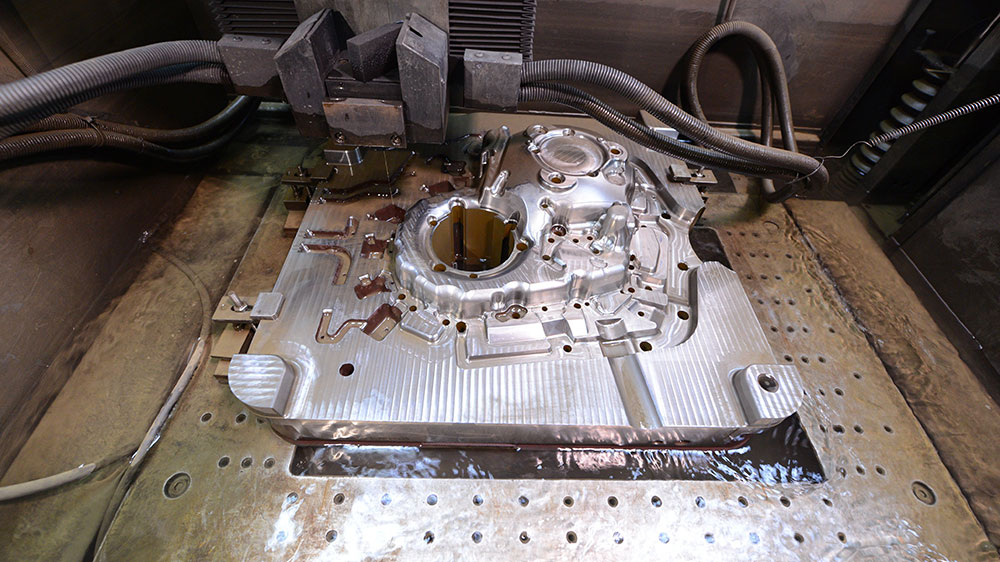
Wspólne wyzwania w oprzyrządowaniu odlewu
Zmęczenie termiczne
- Rozwiązanie: Użyj wysokiej jakości stopów stalowych o lepszej odporności na ciepło.
Metal Flash
- Rozwiązanie: Optymalizuj ciśnienie zacisku i wyrównanie pleśni.
Problemy z porowatością
- Rozwiązanie: Dostosuj ciśnienie wtrysku i czas chłodzenia dla lepszej gęstości.
Wniosek
Narzędzia odlecia die odgrywa istotną rolę w wydajnym wytwarzaniu precyzyjnych i trwałych części metalowych. Niezależnie od tego, czy jest to motoryzacyjne, lotnicze, czy elektroniczne, inwestowanie w wysokiej jakości oprzyrządowanie obsady Die zapewniają doskonałą wydajność i obniżone koszty produkcji.
Często zadawane pytania dotyczące narzędzi odlewu
🛠️ Jakie materiały najlepiej nadają się do oprzyrządowania odlewu?
Oprzyrządowanie odlewającego wymaga materiałów, które mogą wytrzymać ekstremalne warunki, takie jak wysokie temperatury, ciśnienie i naprężenie mechaniczne. Wspólne materiały obejmująStalowa stal narzędzi H13, stopy miedzi, IStal Maraging.
- Stalowa stal narzędzi H13: Znana z wyjątkowej odporności na ciepło i trwałości, stal narzędzi H13 utrzymuje swoją twardość nawet w podwyższonych temperaturach, co czyni ją idealną do przedłużonych cykli produkcyjnych.
- Stopy miedzi: Materiały te są preferowane ze względu na ich doskonałą przewodność cieplną, co pomaga poprawić wydajność chłodzenia podczas procesu odlewania. Szybsze chłodzenie zmniejsza czasy cyklu i poprawia jakość części.
- Stal Maraging: Przy doskonałej wytrzymałości i minimalnym zniekształceniu pod stresem, stal margingowa nadaje się do tworzenia złożonych form, które wymagają precyzji.
Wybór odpowiedniego materiału może zwiększyć długowieczność narzędzi, zmniejszyć wymagania konserwacyjne i poprawić spójność produktu.
❗ Jak mogę zmniejszyć wady w oprzyrządowaniu odlewów?
Minimalizowanie wad w oprzyrządowaniu odlewów dieWłaściwa konstrukcja formy, Kontrola temperatury, IDostosowanie ciśnienia.
- Projektowanie formy: Zapewnienie gładkich ścieżek przepływu materiału, właściwe wentylacja i jednolita grubość ściany zapobiega problemom jak porowatość, skurcz i wypaczenie.
- Kontrola temperatury: Utrzymanie optymalnych temperatur pleśni i materiału zmniejsza naprężenie termiczne, co może powodować pęknięcia lub niepełne wypełnienia. Formy wstępne zapobiegają również nagłym przesunięciom temperatury, które zagrażają jakości.
- Dostosowanie ciśnienia: Zastosowanie odpowiedniego ciśnienia wtrysku zapewnia stopiony metal wypełnia każdą wnękę bez pozostawienia pustek lub kieszeni powietrza. Bilansowanie prędkości wtrysku i ciśnienia optymalizuje integralność części.
Łączenie tych strategii zapewnia lepszą spójność produktu, zmniejszenie kosztów przeróbki i marnotrawstwa materialnego.
📈 Czy narzędzia odlewane są odpowiednie do produkcji o dużej objętości?
Absolutnie! Die Cast Tooling jest znany ze swojej zdolności do wspieraniaProdukcja o dużej objętościzachowując spójną jakość.
- Trwałe materiały narzędzi: Materiały takie jak stal narzędziowa H13 i stal margingowa znoszą tysiące cykli produkcyjnych bez degradacji.
- Wydajne czasy cyklu: Przy precyzyjnej kontroli temperatury i zautomatyzowanych procesach odlewanie matrycy może osiągnąć szybki czas cyklu, poprawia wydajność produkcji.
- Złożona formacja części: Formy odlewane są zaprojektowane tak, aby wytwarzać skomplikowane części z minimalnym przetwarzaniem, co czyni je idealnymi do przebiegów produkcyjnych masowych.
Die obsady narzędzia wyróżniają się w branżach, które wymagają produkcji o wysokim wyjściu, jednocześnie przestrzegając ciasnych tolerancji i szczegółowych specyfikacji.
🚗 Jakie branże najbardziej korzystają z narzędzi odlewu?
Narzędzia odlecia die odgrywa istotną rolę w kilku branżach, w których kluczowe są precyzja, trwałość i skalowalność:
- Przemysł motoryzacyjny: Używany do produkcji komponentów silnika, przypadków skrzyni biegów i części konstrukcyjnych wymagających siły i stabilności wymiarowej.
- Sektor lotniczy: Casting Die tworzy lekkie, ale solidne części, takie jak wsporniki, obudowy i komponenty systemu sterowania.
- Elektronika konsumpcyjna: Władzie cieplne, obudowy złącza i ramy urządzeń korzystają z oprzyrządowania odlewu ze względu na jego precyzję i wszechstronność materialną.
Branże te wykorzystują narzędzia odlewów, aby uzyskać opłacalne, wysokiej jakości komponenty luzem.
Skontaktuj się z nami już dziśAby dowiedzieć się, w jaki sposób nasze rozwiązania oprzyrządowania obsady ekspertów mogą poprawić proces produkcji i poprawić jakość produktu.