Inleiding:
Die cast tooling is een cruciale component in de metaalgietindustrie, bekend van het produceren van complexe geometrieën met hoge precisie en herhaalbaarheid. Deze efficiënte en veelzijdige methode maakt gebruik van herbruikbare mallen om onderdelen te produceren met minimale bewerkingsvereisten.
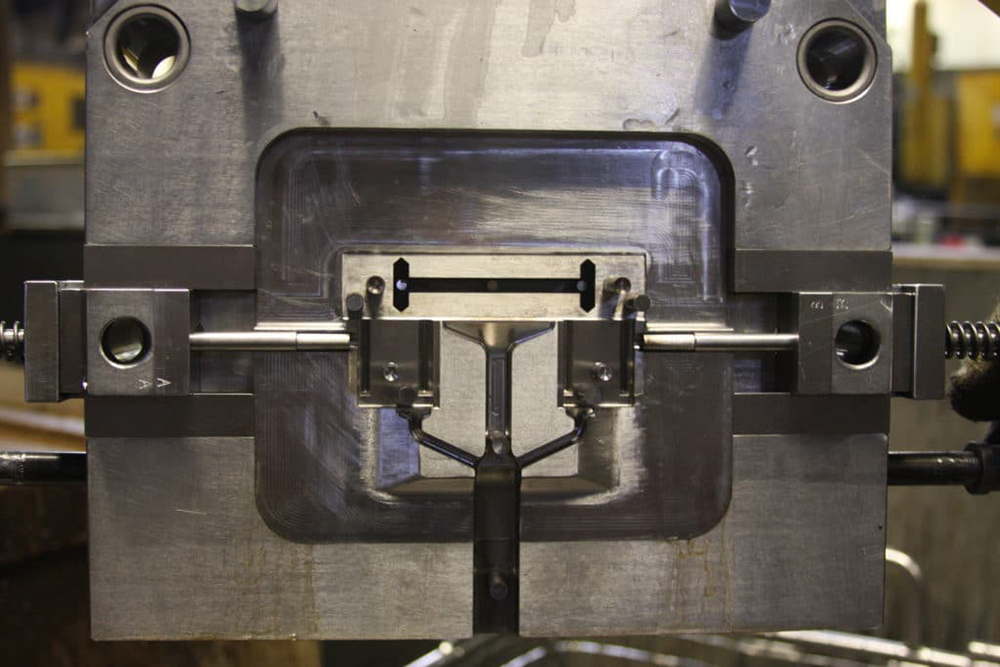
Wat is die gegoten gereedschap?
Die cast toolingVerwijst naar de mallen of gereedschappen die worden gebruikt in het dobbelsteengietproces. Deze vormen zijn ontworpen om metaalcomponenten te creëren door hoge drukinjectie van gesmolten metaal. Belangrijkste materialen die worden gebruikt bij het castgereedschap omvatten:
Die -gietgereedschap is essentieel in industrieën zoals automotive, ruimtevaart en elektronica vanwege het vermogen om gedetailleerde onderdelen efficiënt te produceren.
Stapsgewijze proces van die cast tooling
1. Schimmelbereiding
De fase van de vormbereiding is cruciaal voor het bereiken van castonderdelen van hoge kwaliteit. Het selecteren van het juiste schimmeltype hangt af van uw productiebehoeften. Mogs met één stand van één holte zijn bijvoorbeeld ideaal voor het produceren van één deel per cyclus, waardoor gedetailleerde precisie voor kleinere productieruns wordt gewaarborgd. Ondertussen verbeteren multi-cavity-mallen de productiviteit door meerdere identieke onderdelen tegelijkertijd te maken. Als veelzijdigheid vereist is, staan combinatiemogels meerdere deelontwerpen toe in een enkele vorm. Voor ingewikkelde onderdelen die inzetstukken of dunne wanden vereisen, bieden eenheidsvormen gespecialiseerde oplossingen.
Zodra het schimmeltype is geselecteerd, zijn het reinigen en voorverwarmen van de schimmel essentiële stappen. Reiniging verwijdert verontreinigingen die de stroom van het metaal in gevaar kunnen brengen of in defecten kunnen resulteren. Het voorverwarmen van de mal stabiliseert de temperatuur, waardoor het risico op thermische schok wordt geminimaliseerd, wat scheuren of oppervlakte -imperfecties kan veroorzaken. Deze voorbereiding zorgt voor een optimale metaalstroom en verbetert de duurzaamheid van de mal.
2. Injectieproces
Het injectieproces varieert op basis van het type metaal dat wordt gebruikt. Voor het gieten van de hot kamer, gewoonlijk aangebracht met laagsmeltende metalen zoals zink en magnesium, wordt gesmolten metaal rechtstreeks uit de oven van de machine in de schimmelholte getrokken. Deze methode biedt snelle productiecycli en minimaliseert handmatige hantering, waardoor het ideaal is voor het efficiënt produceren van kleine tot middelgrote componenten.
Daarentegen is koude kamer die casting ontworpen voor metalen met hogere smeltpunten zoals aluminium en koper. Aangezien deze metalen extreme warmte vereisen, moet gesmolten metaal handmatig in de koude kamer worden geleid voordat hij onder hoge druk in de mal wordt geïnjecteerd. Hoewel dit proces iets langer duurt dan de Hot Chamber -methode, zorgt het voor de duurzaamheid en sterkte die nodig is voor grote, robuuste onderdelen die worden gebruikt in veeleisende industrieën zoals automotive en ruimtevaart.
3. Koelfase
De koelfase is van vitaal belang om ervoor te zorgen dat het nieuw geïnjecteerde gesmolten metaal correct stolt in de schimmelholte. Tijdens deze fase blijft de mal gesloten terwijl het metaal afkoelt en in de gewenste vorm wordt verhard. Om krimp te minimaliseren, kan gecontroleerde druk worden uitgeoefend gedurende het koelproces, waardoor uniforme dimensies worden gewaarborgd en de interne spanning in het laatste deel wordt verminderd. Juiste koeltiming is essentieel - als het te snel is gekoeld, kan het onderdeel scheuren of vervormingen ontwikkelen, terwijl overmatige koeltijd de productie -efficiëntie kan verminderen. Het zorgvuldig beheren van de koelfase is de sleutel tot het behalen van consistente resultaten van hoge kwaliteit.
4. Uitvoeding
Zodra het metaal volledig is gestold, moet het onderdeel uit de mal worden verwijderd. Dit wordt bereikt met behulp van ejectorpennen, die de geharde metaalcomponent uit de schimmelholte duwen. Om een soepele uitwerping te vergemakkelijken, nemen schimmelontwerpers vaak concepthoeken op - lichte taps die het onderdeel helpen zonder weerstand vrij te geven. Bovendien minimaliseert de juiste schimmelsmering de wrijving, het verminderen van slijtage op de mal en het verlengen van de levensduur. Ervoor zorgen dat het uitwerpproces naadloos is, is cruciaal voor het voorkomen van schade aan het onderdeel of de schimmel, vooral in productieomgevingen met een hoog volume.
5. Trimmen en afwerken
Eenmaal uitgeworpen, bevat het metalen gedeelte typisch overtollig materiaal dat bekend staat als flits, dat optreedt waar de schimmelhelften elkaar ontmoeten. Dit overtollige materiaal moet worden verwijderd door het snijden, zodat het onderdeel voldoet aan precieze dimensionale toleranties. Afhankelijk van de complexiteit van de component, kan het trimmen handmatig worden uitgevoerd, met behulp van gespecialiseerde snijgereedschappen of via geautomatiseerde processen voor verbeterde efficiëntie. In sommige gevallen kunnen aanvullende afwerkingsstappen zoals slijpen, polijsten of coating nodig zijn om de oppervlaktekwaliteit te verbeteren, de duurzaamheid te verbeteren of het onderdeel voor assemblage voor te bereiden. Goed bijsnijden en afwerken zijn essentieel voor het bereiken van een professioneel, defectvrij eindproduct.
Soorten die gegoten gereedschap
Hete kamer die casting
- Geschikt voor zink-, magnesium- en laagsmeltende metalen.
- Biedt snelle cyclustijden en verbeterde deelintegriteit.
- Vaak gebruikt in elektronica -omhulsels en kleine precisieonderdelen.
Koude kamer sterft gieten
- Ontworpen voor aluminium, koper en andere metalen met een hoog smeltende punt.
- Voorkeur voor het produceren van auto- en ruimtevaartcomponenten.
- Zorgt voor sterkere onderdelen met hogere thermische weerstand.
Functie | Hete kamer die casting | Koude kamer sterft gieten |
Smeltproces | In de machine | Externe oven vereist |
Drukbereik | 1.000 psi tot 5.000 psi | 1500 psi tot 25.000 psi |
Efficiëntie | Snellere cyclustijd | Langere cyclustijd |
Het beste voor | Kleine, gedetailleerde onderdelen | Grote, duurzame componenten |
Voordelen van het gebruik van die cast tooling
- Hoge precisie: Produceert complexe geometrieën met minimale bewerking.
- Kostenefficiëntie: Vermindert materiaalverspilling en stroomlijnen de productie.
- Duurzaamheid: Die gegoten gereedschapsmaterialen zijn bestand tegen intense warmte en druk.
- Oppervlakte -afwerking: Onderdelen geproduceerd met die castgereedschap vereisen minimale afwerking.
Real-World Toepassing van Die Cast Tooling
Case study: auto -industrie
Een autofabrikant gebruikte die castgereedschap om lichtgewicht maar duurzame transmissievormen te produceren. Door koude kamer te gebruiken die met precisiemalen giet, bereikten ze:
- 20% vermindering van materiaalafval.
- Verbeterde thermische prestaties in motoronderdelen.
- Verminderde doorlooptijd met 30%.
Deze succesvolle applicatie onderstreept de rol van die casting -tooling bij het verbeteren van de efficiëntie en productkwaliteit.
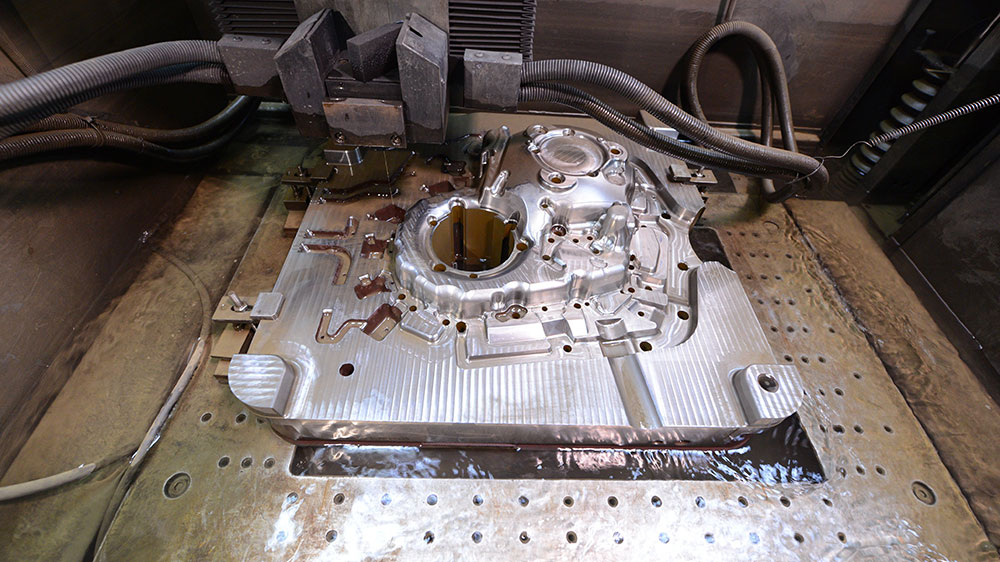
Veel voorkomende uitdagingen in die cast tooling
Thermische vermoeidheid
- Oplossing: gebruik hoogwaardige stalen legeringen met verbeterde warmtebestendigheid.
Metaalflits
- Oplossing: optimaliseer de klemdruk en schimmeluitlijning.
Porositeitsproblemen
- Oplossing: pas de injectiedruk en koeltijd aan voor verbeterde dichtheid.
Conclusie
Die -gietgereedschap speelt een cruciale rol bij het efficiënt produceren van precieze en duurzame metalen onderdelen. Of het nu gaat om automotive, ruimtevaart of elektronica, investeren in hoogwaardige die cast tooling zorgt voor superieure prestaties en lagere productiekosten.
Veelgestelde vragen over die castgereedschap
🛠️ Welke materialen zijn het meest geschikt voor die castgereedschap?
Die gietgereedschap vereist materialen die bestand zijn tegen extreme omstandigheden zoals hoge temperaturen, druk en mechanische stress. Veel voorkomende materialen omvattenH13 Gereedschapsstaal, koperlegeringen, Enstaal.
- H13 Gereedschapsstaal: Bekend om zijn uitzonderlijke hittebestendigheid en duurzaamheid, handhaaft H13 -gereedschapsstaal zijn hardheid, zelfs bij verhoogde temperaturen, waardoor het ideaal is voor langdurige productiecycli.
- Koperlegeringen: Deze materialen hebben de voorkeur voor hun superieure thermische geleidbaarheid, wat helpt bij het verbeteren van de koelefficiëntie tijdens het gietproces. Snellere koeling vermindert cyclustijden en verbetert de onderdeelkwaliteit.
- Staal: Met uitstekende taaiheid en minimale vervorming onder stress is maragingstaal geschikt voor het creëren van complexe mallen die precisie vereisen.
Het kiezen van het juiste materiaal kan de levensduur van het gereedschap verbeteren, onderhoudsvereisten verminderen en de productconsistentie verbeteren.
❗ Hoe kan ik defecten verminderen bij het castgereedschap?
Het minimaliseren van defecten in die cast tooling vereist een strategische aanpak waarbij het gaat omJuist schimmelontwerp, temperatuurregeling, Endrukaanpassing.
- Schimmelontwerp: Zorgen voor gladde materiaalstroompaden, juiste ventilatie en uniforme wanddikte voorkomt problemen als porositeit, krimp en kromtrekken.
- Temperatuurregeling: Het handhaven van optimale schimmel- en materiaaltemperaturen vermindert de thermische spanning, wat scheuren of onvolledige vullingen kan veroorzaken. Voorverwarmende mallen voorkomt ook plotselinge temperatuurverschuivingen die de kwaliteit in gevaar brengen.
- Drukaanpassing: Het uitoefenen van de juiste injectiedruk zorgt ervoor dat gesmolten metaal elke holte vult zonder leegtes of luchtzakken achter te laten. Het in evenwicht brengen van de injectiesnelheid en druk optimaliseert de integriteit van de onderdeel.
Het combineren van deze strategieën zorgt voor een betere productconsistentie, waardoor de kosten en materiaalverspilling worden verlaagd.
📈 Is die gegoten gereedschap geschikt voor productie met een groot volume?
Absoluut! Die cast -tooling staat bekend om het vermogen om te ondersteunenhoogwaardige productiemet behoud van consistente kwaliteit.
- Duurzaam gereedschapsmateriaal: Materialen zoals H13 Gereedschapsstaal en Maragingstaal verdragen duizenden productiecycli zonder afbraak.
- Efficiënte cyclustijden: Met precieze temperatuurregeling en geautomatiseerde processen kan het gieten van die snelle cyclustijden bereiken, waardoor de productie -efficiëntie wordt verbeterd.
- Complexe onderdeelvorming: Die-gegoten vormen zijn ontworpen om ingewikkelde onderdelen te produceren met minimale nabewerking, waardoor ze ideaal zijn voor bulkproductieruns.
Die cast tooling blinkt uit in industrieën die de productie van hoge output vereisen en tegelijkertijd hechten aan strakke toleranties en gedetailleerde specificaties.
🚗 Welke industrieën profiteren het meest van Die Cast Tooling?
Die casting -tooling speelt een cruciale rol in verschillende industrieën waar precisie, duurzaamheid en schaalbaarheid cruciaal zijn:
- Auto -industrie: Gebruikt voor het produceren van motorcomponenten, transmissiegevallen en structurele onderdelen die sterkte en dimensionale stabiliteit vereisen.
- Ruimtevaartsector: Die casting creëert lichtgewicht maar robuuste onderdelen zoals beugels, behuizingen en componenten van het besturingssysteem.
- Consumentenelektronica: Koelputten, connectorbehuizingen en apparaatframes profiteren van die gegoten gereedschap vanwege de veelzijdigheid en de veelzijdigheid van het materiaal.
Deze industrieën maken gebruik van die castgereedschap voor zijn vermogen om kosteneffectieve, hoogwaardige componenten in bulk te leveren.
Neem vandaag nog contact met ons opOm te leren hoe onze expert Die Cast Tooling Solutions uw productieproces kan verbeteren en de productkwaliteit kan verbeteren.